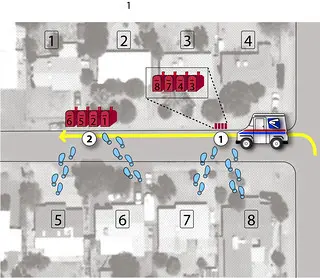
There’s never a bad time to look for ways to eliminate waste from your business supply chain.
The economic turbulence of the past five years undoubtedly prompted businesses big and small to tighten their belts and look for leaner ways of working, but the truth is that every business can benefit from a regular supply chain review.
Commitment to continuous improvement yields even greater rewards.
By building checks and efficiency reporting into the core of your business processes, you can:
- Eliminate waste and unnecessary rework.
- Establish ongoing cost savings.
- Ensure that no potential problem is overlooked for longer than it should be.
- Empower employees to take greater responsibility and ownership of their job.
While the benefits are attractive, there’s a lot of work to be done to get to a fully functional system that removes waste and continues to add incremental changes that make your supply chain more efficient.
Channeling our extensive experience in the field, we’ve compiled eight places that you can begin an efficiency drive for your business.
Before You Start…
First and foremost, you’ll need to decide whether this will be a one-off review to eliminate waste or a holistic commitment to end-to-end development of supply chain efficiency.
We recommend the latter as it reduces cost and resource investment in the long-term. Some business simply won’t be able to allocate the resources for a full scale overhaul, however. If this is true for your organization, a single review that incorporates even just a few of these ideas will prove worthwhile, perhaps laying the groundwork for deeper projects in future.
For those businesses in a position to commit to a continuous improvement program, it’s vital to get buy in from all levels of the organization. From the managers who will be tasked to drive the change to the workers who will provide the indispensable feedback, communications must flow as seamlessly as the the supply chain processes that you will streamline.
Eight Ways to Eliminate Waste from the Supply Chain
1. Start at the end, with the customer
A key part of any waste elimination project is to ensure that it doesn’t detract from the end customer’s experience or satisfaction. They should still receive exactly the same level of service – or ideally much better – that they’ve come to expect from your company. Some improvements will have only internal impacts, which is fine, but there will be others like changes to order fulfillment processes or delivery schedules that can easily affect the customer. Monitor those areas closely for any negative effects before you roll them out across the organization.
On the other hand, customers can also be a useful source of feedback to highlight areas you can improve. Look for common complaints about a specific product or service. If customers in one location complain more often than others, you know there’s a challenge to dive into there. They may also provide comparisons to competitor services, providing you with valuable market insight and a starting point to benchmark your performance.
You can even go so far as to survey a segment of your regular customers to solicit their feedback. Showing this commitment to better serve them can also strengthen the relationship and improve loyalty, making this a win-win approach.
2. Review production lines and administrative processes for unnecessary procedures and rework
As you begin to focus internally, your greatest resource for quick fix ways to eliminate waste is your own workforce. Who better to flag inefficiencies in daily tasks than the people who perform them every day?
Start by conducting a general survey of how each section of your supply chain would rate its efficiency. You can also give workers space on their feedback forms to add specific suggestions or areas of concern. Ask them where they think too much time is spent on any given task. Prompt people to consider why they do a given task and whether it adds value to the overall objective of their role.
Often a simple outlet for expressing opinions will open up a fast flow of issues. This will inevitably include some complaints and criticism (perhaps a lot!) It’s important at this point to be open to hearing any viewpoint, no matter how critical. Solutions are preferable, of course, and required to improve efficiency, but that can’t happen without all the cards on the table. Once all issues are out in the open, prioritization can begin and key areas to eliminate wasteful practices highlighted.
Follow up sessions in small groups will serve to confirm areas of concern and offer a space to begin brainstorming improvements. This can be a unique way to bring staff closer together and offer more control over the job they do.
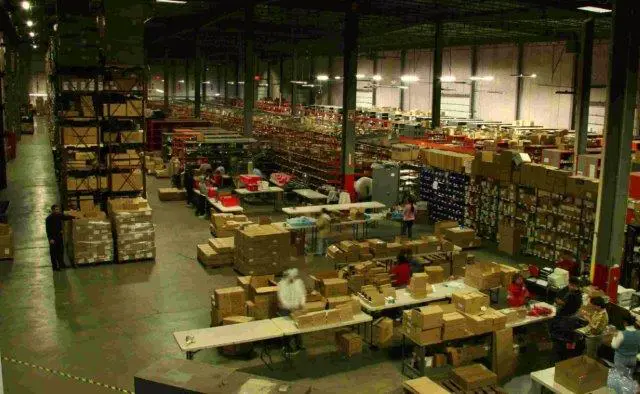
3. Map communication channels to highlight breakdowns
The ways in which your teams communicate need to be as smooth as the physical processes going on around them. To judge how well your business is doing, understanding how information gets from one place to another is the best place to start the ball rolling.
For this you’ll need an expert in process mapping, or at least someone with a head for translating verbal explanations into logical diagrams. If you’re up for the challenge yourself, this primer on mapping will help. It’s also recommended that this be completed as an end-to-end review, so if your time is limited and you want to get more immediate bang for your buck, prioritize some of the other suggestions in this article. That said, these maps will serve a business again and again in future efficiency drives, so it’s worth setting aside the time to create them sooner rather than later.
As you begin to see communications channels emerge, look for diagrams that contain the following:
- Frequent loops in information flow
- Multiple recipients, especially where each is required to sign off for the next step to occur
- Large amounts of information flowing into a single resource (potential bottlenecks)
- Inexplicable gaps or sudden dead ends in communication.
The questions that arise from analyzing these maps will flag areas for improvement. In each case the question should be: “is the right information getting to the right people by the most direct method?”
4. Review equipment and delivery policies
The incremental costs of losses from damage, wasted time and rework often surprise business owners. On its own, a broken pallet or a driver idling at a delivery point for an extra 10 minutes may seem miniscule. Left unattended, however, such waste can easily run into a five or six figure annual expense that could be eliminated from the balance sheet.
Create a list of all the moving parts of your inbound and outbound logistics, highlighting those in particular that you know are high-cost areas. Prioritize those items and any others where performance seems to be below expectations. If you’re at a loss to begin with, consider the following areas for policy and process review:
- Inbound operating hours
- Pallet loss and breakage
- Average delivery lead time
- Average time idle during delivery
- Fuel costs
- Inventory on-hand
- Supplier delivery rates
- Shipping & handling rates
- Ratio of defective parts
5. Bring in suppliers and industry experts for a fresh perspective
Sometimes both business owners and employees are too close to the process to see its shortcomings. Add to that a comfort level that breeds a reluctance to change and you have a clear need for a fresh set of eyes. In this scenario, an outside agent can be the untainted perspective that you need to identify areas for improvement.
Suppliers are a great place to start, as they should be willing to bend over backwards to help you improve your business (and in turn their own). Though they’ll only have the ability to make meaningful input on their area of the supply chain, conducting several feedback sessions of this sort across the supply chain is likely to be a valuable source of inbound analysis.
Have them focus on the points at which their business intersects with your own. Do deliveries run as expected? Are there elements of the relationship that cause them to take on additional responsibilities or rework? If you’ve conducted the communications review from point 3, extend those charts out to the supplier. Are you getting the type of information that you need to keep things moving once they enter your section of the supply chain? There may be additional information that a supplier can provide to ease the flow further down the line.
Bringing in an outside consultant takes things a step further.
By employing someone with experience across all areas of logistics, you can expect to receive advice that improves your entire supply chain. When the full scope of an efficiency drive has your mind spinning, an investment in professional logistics advice is the most effective route to streamlining your operation and reducing cost along the way.
6. Review returns policy and handling
A flexible returns policy is a great customer service differentiator (just ask Zappos customers), but makes efficiency in handling those items even more important. For that reason it’s also a sensible place to focus extra attention when your business wants to reduce waste.
In a similar way to point 3, work on mapping the path of products that return and how they’re handled. Are products for resale moved back into inventory quickly enough? Can defective items be easily returned to your own suppliers and, if so, how quickly are they moving through that process?
Check the quality checks for items that are returned as well. With a liberal returns policy it’s easy for warehouse staff to adopt an equally open approach to returning products into active inventory. This could see defective products floating out for delivery and back for return multiple times, adding no value and potentiallyfrustrating customers.
7. Set up feedback loops and return for regular reviews
Once you’ve been through your chosen waste elimination reviews and taken action on the priority points, it’s worth taking the time to put measures in place that will flag future inefficiencies. After all, why go through all this effort now only to let standards slip again a few months down the line?
The good news is that this is the (relatively) easy bit. Unearthing waste issues and devising better ways of working is the tough part. Once you know what went wrong and have a better process to replace it, the only thing left to do is establish standards for that process. Focus on setting up feedback loops that provide real-time reviews of performance and any new issues that arise. Solving issues as they crop up is the ideal waste elimination approach because it makes it that much more unlikely that things will spiral out of control.
Again, empower employees to develop these feedback systems by asking what they need and providing the required resources to do the job. With an eye on the longer term, establish regular reviews across set intervals (twice yearly or annual usually suffice) to judge how well the new process is doing and iron out any remaining waste concerns.
8. Establish reports and tolerance levels to monitor future waste
A natural follow-on from the previous step, it’s wise to attach weekly or monthly reporting requirements to the new processes you have in place.
Those given the responsibility for monitoring performance should also be tasked with compiling these reports and ensuring that operations remain within acceptable tolerances. This gives your business a kind of early warning system for future failure, allowing quick response and resolution if and when inefficiencies creep back in to the supply chain. On the other hand, creating incentive-based rewards for positive performance helps to stave off those alerts and drive further improvements.
Start with the original objective of the process and work backwards to develop report numbers that tell the truth about how things are going. The focus must be on transparency, encouraging responsibility over blame. Inefficient practices can easily return, perhaps even more covertly if employees feel they are under the microscope. Emphasizing identification and resolution as the only goals of new reporting procedures is important to prevent this from happening.
Each area offers plenty of scope to improve the efficiency of your business and is worth a full article in its own right. We’ll be expanding on these subjects in future posts, so follow our updates on Facebook, Twitter, Google+ or Linkedin to keep up to speed.
And if all this seems overwhelming, fear not! We understand the complexities of managing an effective, efficient supply chain and have decades of experience in all aspects of the industry.